1 、石膏品质不合格的主要原因
石膏购买商对石膏的品质验收要求见表1。

东方电厂脱硫系统在投产运行初期,经常会出现石膏品质不合格的现象,
脱硫石膏品质分析指标见表2。

分析几次石膏品质不合格的运行工况,发现大多是在满负荷工况下,原烟气SO2含量在3000mg/ m3以上时,会出现吸收塔密度居高不下、石膏脱水效果不好的情况,通过对其相关运行控制指标分析,发现有以下几个方面因素影响石膏品质。
1.1 运行工况远偏离脱硫系统的设计值
1.1.1 高负荷时入口原烟气二氧化硫浓度超设计值
电厂脱硫系统机组满负荷运行,入口原烟气二氧化硫浓度达到4000mg/Nm3(设计入口原烟气二氧化硫浓度3393mg/Nm3),入口烟温高达160℃(设计入口烟温为123℃)。吸收塔密度高,真空皮带脱水机上的石膏成黑色泥状,脱水困难,脱硫石膏含水量高,亚硫酸盐含量高(23.8%),原因为进入吸收塔的二氧化硫处理量增大,远远超过了设计工况,造成吸收塔吸收及氧化效果不佳,亚硫酸盐含量大,不易脱水,石膏品质不合格。
1.1.2 入口原烟气温度超设计值
设计入口烟温为123℃,但由于省煤器及空气预热器设备设计缺陷,入口烟温高达165℃,造成脱硫系统吸收效果不好,脱硫效率下降,烟囱入口二氧化硫浓度升高。为保证满足环保排放要求,吸收塔pH值控制较高,高pH值控制不利于氧化反应的进行,石膏结晶效果不好,亚硫酸盐向硫酸盐氧化比例不大,不利于脱水。
1.1.3 入炉煤发热量比设计值低
设计入炉煤发热量为5300kJ/kg,锅炉用煤量为129t/h,而实际入炉煤发热量为4900kJ/kg,锅炉实际用煤量在145t/h 左右。由于设计煤种发热量高,造成原煤量增加10%以上;同时原烟气流量增大,单位时间内处理二氧化硫量大,超出脱硫系统的处理能力,运行一台氧化风机(一用一备) 的氧化效果不好,吸收及氧化充分反应条件不满足,造成吸收塔石膏浆液氧化不彻底,浆液亚硫酸根含量超标,石膏结晶时间过短,石膏过饱和度达不到1.3左右的要求,石膏滤饼品质差,脱水困难。
1.2 入炉煤的配烧受限
受原煤供应(煤源不稳定,来煤矿点多,煤种较杂)和煤场容量偏小堆(燃煤分类存放空间受限)影响,运行的配煤掺烧受到限制;特别是在煤场存煤较少时,配煤工作无法进行,造成有时煤场只有含硫量低但发热量也低的印尼煤,有时又只有含硫量高而发热量低的平朔煤,燃烧时烟气处理量大。在燃烧高含硫量低发热量平朔煤时,脱硫系统无法适应满足处理能力,造成石膏品质不合格。
1.3 电除尘设备除尘效率较低
电除尘设备运行模式有节电模式一、节电模式二和火花跟踪三种,从运行经济性考虑,电除尘常在节电模式下运行,相对除尘效果差,石膏中粉尘杂质含量高。
1.4 旋流子出力不足
由于机组运行时的工况与设计条件下的相差甚远,石膏旋流器只安装五个旋流子,四运一备,留有一备用孔;但在系统负荷高、原烟气含硫高时,石膏产量大,脱水机24h运行吸收塔密度仍然居高不下,石膏旋流器满足不了生产需要。
2、 处理对策
2.1 入口烟气控制
通过调整煤场容量和配煤掺烧、提高省煤器和空气预热器换热性能、提高电除尘效率和减少设备故障,电厂分别控制入口烟气的二氧化硫浓度、入口烟气温度和粉尘含量,具体措施如下。
2.1.1 调整煤场容量和配煤掺烧
要求燃料供应部门根据现场情况提供可掺烧的煤种,加快二期圆形煤场的施工建设,保证煤场存煤量足够,通过加强现场配煤掺烧控制入炉煤发热量和含硫量,以满足脱硫系统设计的运行工况,保证烟囱入口二氧化硫排放浓度合格。
2.1.2 提高省煤器和空气预热器换热性能
对省煤器和空气预热器进行改造,增加省煤器管圈、更换空预器热端传热元件,增加换热面积50%。#1炉改造后排烟温度比考核试验时低了12.3℃左右,#2炉改造后排烟温度比考核试验时低了18℃左右,烟温从改造前的160℃左右降到145℃左右,大大降低了入口烟温,使得吸收塔内反应容易控制,吸收效率大大升高。
2.1.3 提高电除尘效率和减少设备故障
在保证环保排放的前提下选定电除尘的投运模式,提高电除尘器除尘效率。提高检修对设备的消缺率,减少除灰设备故障、避免锅炉燃油或避免电除尘连续振打所引起的二次飞扬造成的粉尘含量增加,降低石膏中粉尘含量。
2.2 脱硫系统运行控制
2.2.1 浆液pH值的控制
湿法脱硫工程的运行经验表明,在其它参数基本稳定的工况下,升高浆液pH值即增加石灰石浆液量,可在一定程度上提高脱硫效率。但若长时间保持高pH运行,会导致石膏中未完全反应的CaCO3和CaSO3含量增加,品质下降;因为当pH>5.9时,石灰石中Ca2+的溶出速度会减慢。同时,当pH>5.9时SO32-的氧化也受到抑制,因为SO32-氧化的最佳pH在4.5~4.7 (如图1所示),此环境下只要鼓入足够的氧化空气,SO32-几乎可以全部氧化,而且此范围pH同时也是石膏结晶的最佳pH环境。但较低值的pH会使SO2的吸收受抑制,若pH为4.0,SO2几乎不被浆液吸收,而且加剧了设备的腐蚀。因此工艺控制中必须兼顾烟气脱硫和SO32-氧化对浆液pH的要求。
图1 pH对SO32-氧化速率的影响
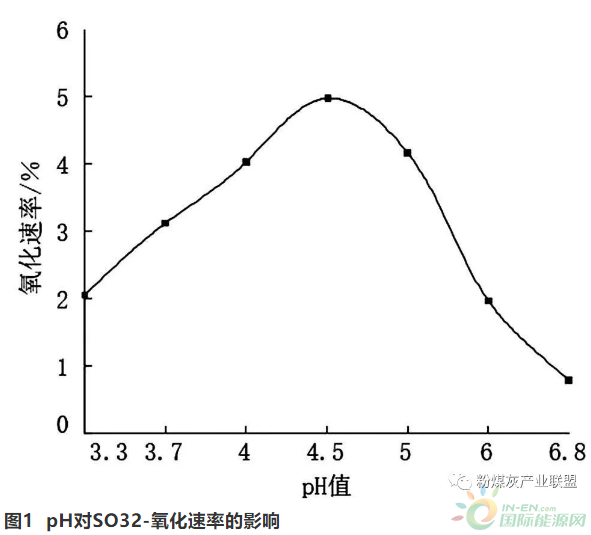
同时,当出现吸收塔烟气量增加较多、含硫量增加时,可通过适当添加脱硫增效剂加强对煤种的适应性,加快吸收化学反应过程,增强石灰石的溶解特性,降低吸收塔运行pH值,从而有利于氧化反应的进行,石膏品质得到较大的改善。
2.2.2 保证亚硫酸钙的氧化效果
在含硫量高及石膏脱水困难时,保持合适的pH值,间断地启动两台氧化风机保证氧化效果,使脱硫反应中生成的亚硫酸钙(CaSO3)氧化为硫酸钙(CaSO4),并生成石膏(CaSO4 · 2H2O)晶体,通过控制石膏过饱和度在1.3左右,保证石膏结晶成粗棒状晶型,使得石膏具有良好的脱水性能。
2.2.3 控制吸收塔浆液密度
在机组负荷高、原烟气二氧化硫浓度高时,吸收塔浆液密度达到1130kg/m3时,启动真空脱水系统和石膏排浆泵,尽早做好降低吸收塔浆液密度的措施。
2.2.4 安装备用孔旋流子
在石膏旋流器的备用孔加装一个旋流子,当出现吸收塔密度大幅升高、居高不下时,可通过运行六个旋流子(设计为四用一备),加大石膏的产出量,有效地降低吸收塔石膏浆液密度。
2.2.5 加强脱硫废水系统投运以及维护工作
原烟气中HCl、HF和飞灰都会进入吸收塔浆液中;长期运行后,吸收塔浆液的氯离子和飞灰中不断溶出的一些重金属离子浓度会逐渐升高,从而对SO2的吸收反应产生负面影响。所以在废水系统设备正常的情况下,启动脱水系统时必须启动脱硫废水系统,加大对吸收塔内氯离子以及其他杂质离子的排放,为产出好品质石膏创造良好的内部环境。
2.2.6 在线仪表的定期标定
要求检修部门定期对脱硫系统中SO2分析仪、粉尘含量测试仪、pH计、吸收塔液位计、浆液密度计等在线仪表定期标定,保证运行控制参数的准确;运行人员及时调整运行工况,控制吸收塔内的吸收氧化结晶化学反应条件,保证环保指标达标排放,不发生影响环保形象的事件,顺利通过环保核查。
2.3 加强环保实验室分析工作
加强对石灰石粉的采样频度,每周对采的总样分析一次,对石灰石粉的纯度和细度进行分析,保证在验收合格指标范围内。另外,每天对石膏浆液进行pH值、密度化学分析,比对校准现场在线仪表,供运行调整参数时参考。